Understanding Control Valves: What They Are and Why They Matter
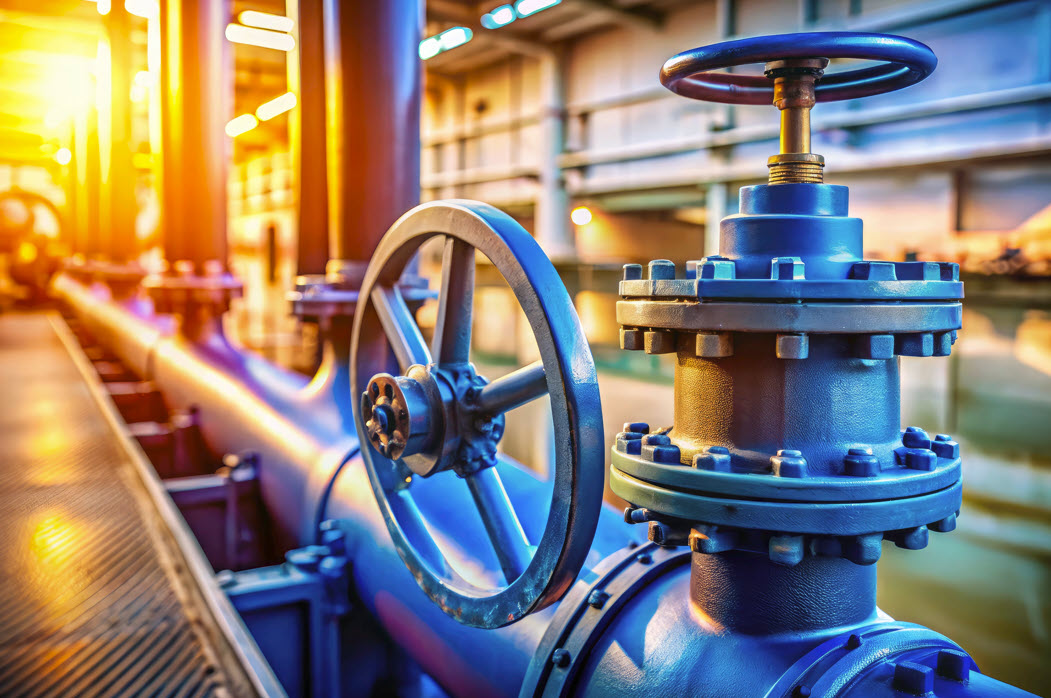
Flow control valves are essential components in various industrial and hydraulic systems, playing a critical role in regulating the flow rate or pressure of fluids and gases. They allow systems to operate efficiently and safely, thereby preventing potential damage and maintaining optimal performance.
Whether you’re managing a maintenance team or overseeing operational systems, understanding what flow control valves are and why they matter can help you make smarter decisions for your facility.
Already up to speed on control flow valves and want to explore your options? You can find them here.
What Is a Flow Control Valve?
A flow control valve is a device used to regulate the flow of fluids – such as liquids, gases, or steam – within a system. By managing the flow rate and pressure, these valves ensure that your machinery and processes function as intended. That makes flow control valves vital in industries ranging from food processing and pharmaceuticals to automotive manufacturing and oil refining.
These valves come in various forms to suit different applications. Manual valves require hands-on adjustment, while automated systems use sensors and actuators for precise control. For instance, an electric flow control valve might adjust fluid rates based on data from a connected monitoring system, optimizing operations without human intervention.
Flow control valves not only manage flow but also help maintain system stability, prevent leaks, and improve overall safety, making them indispensable in any industrial setup.
How Flow Control Valves Work
At their core, flow control valves regulate the passage of fluid by altering the size of the pathway. The mechanism varies depending on the design and application, but the principle remains the same: controlling the flow to meet system requirements.
Take, for example, a hydraulic valve in heavy machinery. When the system requires more power, the valve widens the pathway to increase fluid flow. Conversely, during low-demand periods, the valve constricts the flow, conserving energy and reducing wear on equipment.
Key components include the body, orifice, and actuator, each of which plays a crucial role in the valve’s operation. In automated systems, actuators respond to real-time data from sensors, ensuring optimal performance even in dynamic conditions. This seamless adjustment is especially critical in high-stakes industries like aerospace and chemical manufacturing, where precision is paramount.
Choosing the Right Flow Control Valve for Your Needs
Selecting the right valve involves more than picking one that fits your system. It’s about understanding the specific demands of your application. For example, does your system handle corrosive materials? Then you’ll need a valve made from corrosion-resistant materials like stainless steel or specialized alloys. Are you working with high temperatures or pressures? If so, ensure the valve is rated to withstand those conditions.
Automation is another key consideration. While manual valves might suffice for straightforward applications, automated valves provide higher accuracy and are often more cost-effective in the long run. Automated systems can adjust to varying conditions instantly, reducing the risk of system downtime and operational inefficiencies.
Proper sizing is critical as well. A mismatched valve can cause pressure drops or turbulence, both of which impact system performance. Consulting with a supplier who understands your industry can help ensure you select the ideal valve for your setup.
Types of Flow Control Valves
There are several types of flow control valves, each used for specific applications. Understanding the various options can help you select the right valve. Common types include:
- Needle Valves. Needle valves feature a needle-shaped plunger that precisely controls flow by moving in and out of a seat. These valves are ideal for applications requiring fine adjustments, such as in instrumentation, flow metering systems, and scenarios where precision is critical.
- Globe Valves. Globe valves have a globe-shaped body and a disc that moves up and down to regulate the flow. They are commonly used for general-purpose flow control. This particular design allows for more accurate flow control compared to other valve types, which makes them suitable for applications where throttling is necessary.
- Ball Valves. Ball valves use a rotating ball with a hole through it to control flow. By turning the ball, the valve can quickly switch between fully open and fully closed positions. Known for durability and tight sealing, ball valves are often used where a quick shut-off is required, such as in piping systems and water treatment plants.
- Butterfly Valves. Butterfly valves operate with a disc that rotates within the pipe to regulate flow. These valves are particularly useful in large-diameter pipelines due to their compact design and ease of operation. Butterfly valves are commonly found in water distribution, HVAC systems, and large industrial applications.
- Other Types. Other flow control valves include diaphragm valves and plug valves, each having its own unique characteristics and specific uses. For example, diaphragm valves are suitable for handling corrosive or viscous fluids, while plug valves offer reliable shut-off capabilities in high-pressure applications.
Flow control valves are not just components; they are investments in the efficiency, safety, and profitability of your operation. Here’s why they matter:
First, they help maintain consistent product quality. In industries like food and beverage production, even slight variations in flow can affect the taste or texture of a product. Flow control valves ensure that every batch meets strict quality standards.
Second, they enhance energy efficiency. By optimizing fluid movement, these valves reduce unnecessary energy consumption, lowering operational costs over time. This is especially significant in large-scale operations where small inefficiencies can add up quickly.
Finally, they promote equipment longevity and workplace safety. By regulating pressure and flow, valves minimize wear and tear on machinery, reducing the likelihood of costly repairs or replacements. Proper flow control also prevents hazardous situations, such as sudden pressure surges, that could endanger employees or damage equipment.
Addressing Common Challenges with Flow Control Valves
Like any mechanical component, flow control valves come with challenges. Blockages from debris or sediment can obstruct flow, reducing efficiency. Pressure surges caused by sudden changes in flow can damage equipment. Regular maintenance is critical to addressing these issues and keeping systems operational.
To prevent blockages, consider using valves with self-cleaning features or installing filtration systems upstream. For pressure surges, look for valves with built-in pressure relief mechanisms. A robust maintenance schedule, including inspections and cleanings, will ensure that your valves perform optimally and extend their lifespan.
How to Find the Right Supplier for Flow Control Valves
The performance of your flow control valves starts with the quality of the product and the expertise of your supplier. A good supplier will offer more than just a catalog of options—they’ll provide tailored recommendations based on your specific needs.
Look for suppliers with a strong track record in your industry. They should offer a wide range of valves, from manually operated models to state-of-the-art automated systems. High-quality products come with certifications and warranties, giving you confidence in their performance.
ACI Controls supplies flow control valves that meet the rigorous demands of manufacturing facilities across the U.S. We take pride in helping our clients find the right solutions, ensuring optimal performance and long-term reliability.
Flow Control Valves: A Small Component with Big Impact
The right flow control valve can be a game-changer for your operation. From improving product quality to enhancing safety and efficiency, these components play a vital role in keeping your systems running smoothly. By understanding how they work and what to look for in a valve, you’re equipped to make better decisions for your facility.
Ready to take your operations to the next level? Contact us today to explore our selection of high-quality flow control valves and find the perfect fit for your needs.